Ultrahøyytelsesbetong Er Klar Til Å Revolusjonere Prefabrikert, Forspent Betong
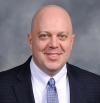
ultra-high performance concrete (UHPC) utvikler seg raskt som et førsteklasses materiale for prefabrikert betongkonstruksjon. Først introdusert som «reaktivt pulverbetong» tidlig på 1990-tallet, har dette materialet sett økende bruk i USA og i utlandet det siste tiåret.
UHPC har blitt brukt til å bygge veibroer I Frankrike, Japan og Malaysia; fotgjengerbroer I Canada og Venezuela; takpaneler og arkitektoniske fasader I Canada og Frankrike; og mer.
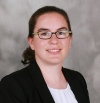
I USA HAR UHPC blitt brukt til å konstruere brobjelker I Virginia og Iowa, brodekkoverlegg I New York og Delaware, og feltstøpte ledd mellom prefabrikerte bromedlemmer i mer enn 20 andre stater. Pågående forsknings-og utviklingsarbeid av føderale og statlige transportbyråer, nasjonale bransjeorganisasjoner, private eiere og betongprodusenter søker å fremme denne teknologien ytterligere, slik at den kan bli bredere vedtatt i både transport – og byggebransjen.
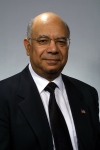
en nøkkelindustri som er velegnet til å utnytte de unike ytelsesegenskapene til dette materialet, er prefabrikert forspent betongindustri.
HVA ER UHPC?
UHPC ER et fiberforsterket, sementbasert materiale. Den inneholder mange av de samme materialene som konvensjonell betong-sement, supplerende sementbaserte materialer (Scm), fin sand og kjemiske tilsetninger — men materialene er proporsjonert for å skape en tett pakking av materialer fra silikafume til sand, dvs.fra de fineste til de groveste materialene.
Samlet innhold av sementholdige materialer for UHPC-blandinger kan og ofte overstige 1500 lbs per cu yd av materiale – mer enn dobbelt så mye som innholdet av sementholdige materialer i de fleste konvensjonelle betongblandinger. Imidlertid er vann-til-bindingsforholdet (w / b) ofte 0,20 eller mindre, lettere ved bruk av spesialvannsreduksjonsapparater med høy rekkevidde. Den tette partikkelpakningen, kombinert med den ultra-lave w/b, skaper i betongen en svært raffinert mikrostruktur som gir eksepsjonell styrke og holdbarhet. SOM ET resultat KAN UHPC-elementer ha en forventet levetid på 200 år eller mer, selv i krevende miljøer som marine-og avising-eksponeringer.
selv om det ikke er noen enhetlig avtalt definisjon AV UHPC, er typiske UHPC-trykkstyrker over 17 000 psi, med mange kommersielt tilgjengelige UHPC-materialer som kan oppnå styrker på 30 000 psi eller mer. SAMMENLIGNET med konvensjonelle og høyytelsesbetong, KAN UHPC gi en 3 til 5 ganger økning i trykkstyrken. Trykkstyrken er imidlertid ikke den viktigste egenskapen til dette materialet. En viktig differensiator mellom strukturelle UHPC og andre klasser av betong, spesielt for strukturelle prefabrikkerte applikasjoner, er materialets høye strekkytelse, som kommer fra en kombinasjon av den raffinerte mikrostrukturen og de høyfaste stålmikrofibre som er innlemmet i blandingen ved doser mellom ca.1 og 3%, i volum (ca. 130 til 390 lbs/cu yd).
STRUKTURELLE UHPC-blandinger kan utformes for å oppnå direkte strekkstyrker på mer enn 1000 psi, og bøyestyrker på mer enn 2500 psi. Videre kan en veldesignet UHPC-blanding utvise betydelig post-cracking duktilitet og belastningsherding, noe som øker gjenværende bøyestyrke betydelig ettersom elementet avbøyer etter sprekkdannelse.
DEN høye strekkfastheten og duktiliteten ETTER cracking AV UHPC gir betydelig fordel for strukturell design. For det første kan post-cracking duktilitet og belastning herding atferd tillate virtuell eliminering av minimum armeringsstenger som kreves i konvensjonell betong for å oppnå kode-mandat duktilitet når svikt er nært forestående.
For Det andre resulterer DEN høye duktiliteten TIL UHPC i en enorm material seighet, noe som øker evnen til å absorbere energi selv uten hjelp fra armeringsstengene.
For Det Tredje øker den høye strekkstyrken materialets skjærmotstand, med mulighet for total eliminering av skjærbøyler i stråledesign. Ved å eliminere stigbøyler, element design og produksjon kan forenkles, og medlem web (stem) bredder kan reduseres. Faktisk kan bjelker, kolonner og ANDRE UHPC-strukturelle medlemmer utformes med tverrsnitt som har mye mindre volum og dermed vekt av materiale, samtidig som de gir samme kapasitet som konvensjonelt armerte betongelementer.
Avansert Teknologi for Prefabrikert, Forspent Betong
UHPC viser betydelig løfte om å fremme egenskapene til prefabrikert, forspent betongindustri. Ytelseskarakteristikkene til dette materialet kan tillate utforming av strukturelle systemer som opprettholder akseptabel styrke og brukbarhet, samtidig som de har reduserte medlemsvekter, utvidede spennlengder og mindre forsterkende. Videre, med den høye holdbarheten som dette materialet gir, kan disse strukturelle systemene brukes i krevende miljøer, for eksempel marine applikasjoner og eksponering for kaldt vær, som lav kostnad / nytte-forhold alternativer til design som bruker rustfritt stål og ikke-metalliske armeringsstenger.
FOR AT UHPC skal kunne se utbredt implementering i prefabrikert forspent betongindustri, må to betingelser være oppfylt: (1) UHPC må kunne produseres pålitelig på prefabrikerte anlegg, med råvarekostnader på totalt mindre enn $1000 per cu yd (sammenlignet med nåværende kostnader på $2000 til $3000 per cu yd for pre-bagged materialer); og (2) prosedyrer må utvikles for å muliggjøre design av strukturelle systemer som utnytter de unike ytelsesegenskapene av uhpc. Slike prosedyrer kan gi enorm verdi ved å muliggjøre omtrent 50% reduksjon i tverrsnitt sammenlignet med konvensjonelle betongprodukter.
Precast/Forspent Concrete Institute (PCI) har anerkjent dette behovet og viet ressurser til å støtte et forskningsprosjekt til fordel for industrien. Den overordnede prosjekt og design retningslinje utvikling blir ledet av e. construct Of Omaha, Neb., mens materialets aspekter av prosjektet har blitt ledet av to av forfatterens firma, Wiss, Janney, Elstner Associates Of Northbrook, Ill.
de primære målene for dette prosjektet er å utvikle metoder for å implementere kostnadseffektive UHPC-blandinger basert på lokalt tilgjengelige materialer på precaster-anlegg i Hele Nord-Amerika og å utvikle designretningslinjer og nye design for optimaliserte strukturelle medlemmer for bygninger og broer.
til dags dato har prosjektgruppen utviklet retningslinjer og anbefalinger for utforming OG implementering AV UHPC-blandinger ved prefabrikkerte forspente betongproduksjonsanlegg og har validert disse prosedyrene gjennom produksjon ved fem slike anlegg OVER HELE USA (Se Figur 1 FOR EKSEMPEL UHPC-plassering på en av de deltakende precasters).
i tillegg er prototyper av langspennede bro-og bygningselementer designet, produsert og testet av prosjektteamet, med de ultimate medlemsstyrkene som overstiger designbelastningen. Det forventes at til tross for den opprinnelige høye prisen PÅ UHPC-materialene, vil de optimaliserte designene og reduserte medlemstverrsnittene gjøre DISSE UHPC-produktene konkurransedyktige med konvensjonelle betong – og stålalternativer på en innledende kostnadsbasis. Fremgangen til dags dato er oppsummert I En Fase i-rapport publisert i februar.
Figur 1. Plassering AV UHPC, som viser selvkonsoliderende konsistens.
Eksempelapplikasjoner Av Optimaliserte UHPC-Medlemmer
VED HJELP AV UHPC er det nå mulig å designe kontorbygggulv med kolonnefrie bukter som er 60 fot med 60 fot, noe som gir stor fleksibilitet i interiørdesign av leid plass. Det er også mulig å bygge brobjelker så lenge som 250 ft, innenfor akseptable frakt-og ereksjonsgrenser, og uten behov for feltstøtte eller spleising. De følgende to eksemplene illustrerer DET sterke potensialet I UHPC-applikasjoner.
Figur 2 viser et designkonsept for bruk i bygninger. Det» π » formede tverrsnittet er et prefabrikert, forspent gulvpanel som gir mulighet for en 60-ft span med en dybde på 22 tommer. Ingen stål, annet enn forspenningsstrengene, er nødvendig for dette designet. Den øverste flensen er bare 1-tommers tykk og stilkene er bare 2-inches bred. Den totale vekten tilsvarer en solid plate mindre enn 3 tommer tykk. Installert, bjelkelaget ville være lukket inn med lys gage bjelkene strekker seg mellom stilkene og dekket med gipsplater, og stilkene har åpninger for å tillate integrering av verktøy. Med dette langvarige produktet kan boligbygg med flere etasjer ha kolonnefri parkering i de nedre etasjene, noe som forbedrer effektiviteten av plassutnyttelsen og sikkerheten til beboerne. Den relativt grunne strukturdybden-med de mekaniske, elektriske og vvs-systemene-sørger for effektiv bruk av plass og kostnadseffektiv historiehøyde.
Figur 2. KONSEPTET MED EN UHPC Skive System for Bolig applikasjoner
Figur 3 viser en konvensjonell betongplate bjelke brukes for 40-til 60-ft spenn i akselerert bridge construction (ABC) applikasjoner. Figuren viser også en optimalisert UHPC-kasseplate med samme dybde, bredde og lastekapasitet. UHPC-produktet har omtrent 52% av betongen og mindre enn 4% av armeringen, sammenlignet med den tilsvarende konvensjonelle betongbjelken. Fullskala testing Av Florida DOT Structural Laboratory viste at denne stråledesignen har mye høyere bøyning, skjær, stanseskjær og tverrkapasitet enn nødvendig for broen. Ytterligere forbedringer i elementutformingen kunne rettferdiggjøre en reduksjon i antall tråder som ble brukt, som ble holdt på samme måte som for det konvensjonelle betongproduktet for denne demonstrasjonen.
Figur 3. Boks skive for bro applikasjoner. Venstre: konvensjonell betongboksplate som viser forsterkning( før forskalingsinstallasjon); Høyre: optimalisert UHPC box slab (med forskaling og skum void-forming blockout på plass).
Konklusjon
UHPC har potensial til å revolusjonere prefabrikert, forspent betongindustri, spesielt i store applikasjoner, hvor lange spenn eller forbedret holdbarhet er gunstig. MED nye design og nye designprosedyrer har UHPC muligheten til å være kostnadseffektiv med konvensjonelle betong-og stålalternativer på førstekostnadsbasis, og kan gi ytterligere verdi på en langsiktig livssykluskostnadsbasis. Ved å dra nytte av de viktigste egenskapene I UHPC, vil langspennede prefabrikkerte bro-og bygningsmedlemmer revolusjonere industrien, gjennom mer effektiv bruk av materialer, forbedret plassutnyttelse og forbedret langsiktig ytelse.